We are Here To Serve You
Chad Root and Manny Diaz, long-time Fast Heat employees, founded Spark Industries in December 2020 in order to acquire Fast Heat’s remaining product lines in the injection molding industry – hot runner controls, mold checkers, cable checkers, mold boxes, cables and service. You can expect personalized, hands-on shop-floor trials, training, service, spare parts support and guidance.
“Manny and I met while working at Fast Heat. Sparky was our mascot in the front lobby. We always thought he was pretty cool so when we needed to start a company to acquire Fast Heat’s product line, we named it Spark”
Chad Root, Managing Partner
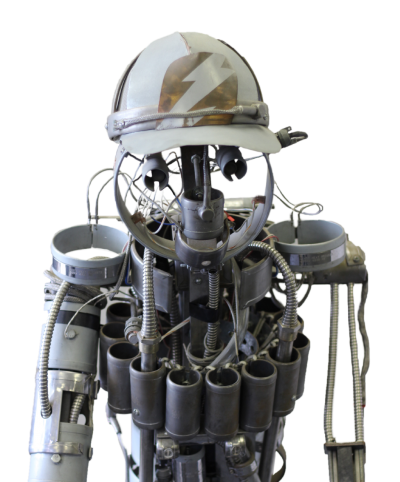
Our History
Hot Runner Control Testimonials
The current hot runner control platform was launched in 2003-2005 during a competitive time in our industry. We earned a reputation for practical and straightforward high-tech solutions. Our advanced temperature control technology enables molder to tackle finicky materials, thin walls, complex geometries and tight gate vestiges.
We’re Reliable…
“We knew we needed an integrated controller but were concerned about the higher purchase price over our modular box units. The Pulse Controller fit our needs because it was affordable and offered advanced technological features that save us time and money. Our personnel have all commented on how easy they are to use and that they are reliable.”
“I prepared a very detailed product comparison between the Pulse and another leading integrated controller. We decided to buy the Pulse because it met our technical requirements and was easier to use. Fast Heat also supplied a trial unit in much less time.”
We’re Precise…
“We need Pulse to achieve the critical gate temperature control required to mold thin-wall parts with challenging part geometries.”
“We bought our first Pulse controller because of the improvements we would see in mold and controller maintenance. We continue to realize those savings as well as savings in production set-up and ease-of-use. Our other Plant Managers are taking notice.”
“We had a problem molding Santoprene onto a pre-molded polypropylene part. We were experiencing inconsistency in part quality, ranging from short-shots to flashing. Fast Heat supplied a 12-Zone Controller. We immediately began producing quality finished parts.”
We’re Efficient…
“Feedback from Waterfall/Energy Study: ‘Great news. The CPK data shows that parts molded using the Pulse were 12 percent closer to the mean on average. All parts were in tolerance (both controllers) but the ID in the critical dimension area varied 12 percent above and below the reference point with the MSI controller. Doesn’t sound like much but that number is huge when you look at the mating part and how it must fit.”
“The most important factor for us is how simple it is to use. Everything is easy to get to and modify. We don’t have to spend a lot of time setting it up or using it. The Pulse is also more efficient than other controllers by the way it provides power.”
We’re Flexible…
“When our local government mandated that all equipment be certified to special electrical requirements, Fast Heat is the only company who responded and carried through on their commitment. We are buying our next controller from Fast Heat.”
“The controller is great!! We have not had any of the issues with this tool like we were seeing before.”
Processing Improvements:
- Easily work with hard-to-run materials including Nylon 6-6, Santoprene (TPEs) and wide-spec regrinds.
- Produce high quality hard-to-run parts that have thin walls, small sizes, co-injected or over molded.
- Eliminate most stringing and burning situations attributed to temperature control.
Industries Served:
- Appliance
- Automotive / Heavy Truck
- Consumer
- Medical
- Military
- Packaging