MOD24™
COMING Q1 2025! – MOD24™ is our latest innovation in hot runner control. This patent-pending, modern, modular hot runner controller offers unlimited modularity of 6-zone hot runner control modules within 24-zone cabinets up to 192-zones. Use with our Pulse display, either cabinet mounted or remote mounted or easily integrate with your injection molding machine control via OPC-UA or VNC Viewer.
Isn’t it time to replace those old modular controllers that require individual settings and control by zone while offering limited additional capabilities? It’s time to Trade-Up for 2025!
- Modern Technology for Improved Processing, Energy Savings, and Diagnostics
- Simply Select a Recipe and Run While Protecting Your Tools
- Plug-N-Play Modules and Cabinets for Easy Expansion
- Compact and Flexible Use as Table-Top, Mobile Rack, or Wall Mount
- Best of Both Worlds – Integrates with molding machines via OPC-UA, VNC Viewer, and I/O while easily being deployed at other machines when needed.
- Industry Leading Ease-of-Maintenance and Diagnostics Along with Our MoldXChecker® and CableXChecker®
Please complete this form with a description of the modular style controller/s you are interested in trading in. We accept ALL BRANDS, not just Fast Heat—the trade-in value shows as a discount on a quote for a new MOD24 configuration. Or – give us a call at 574-606-4243.
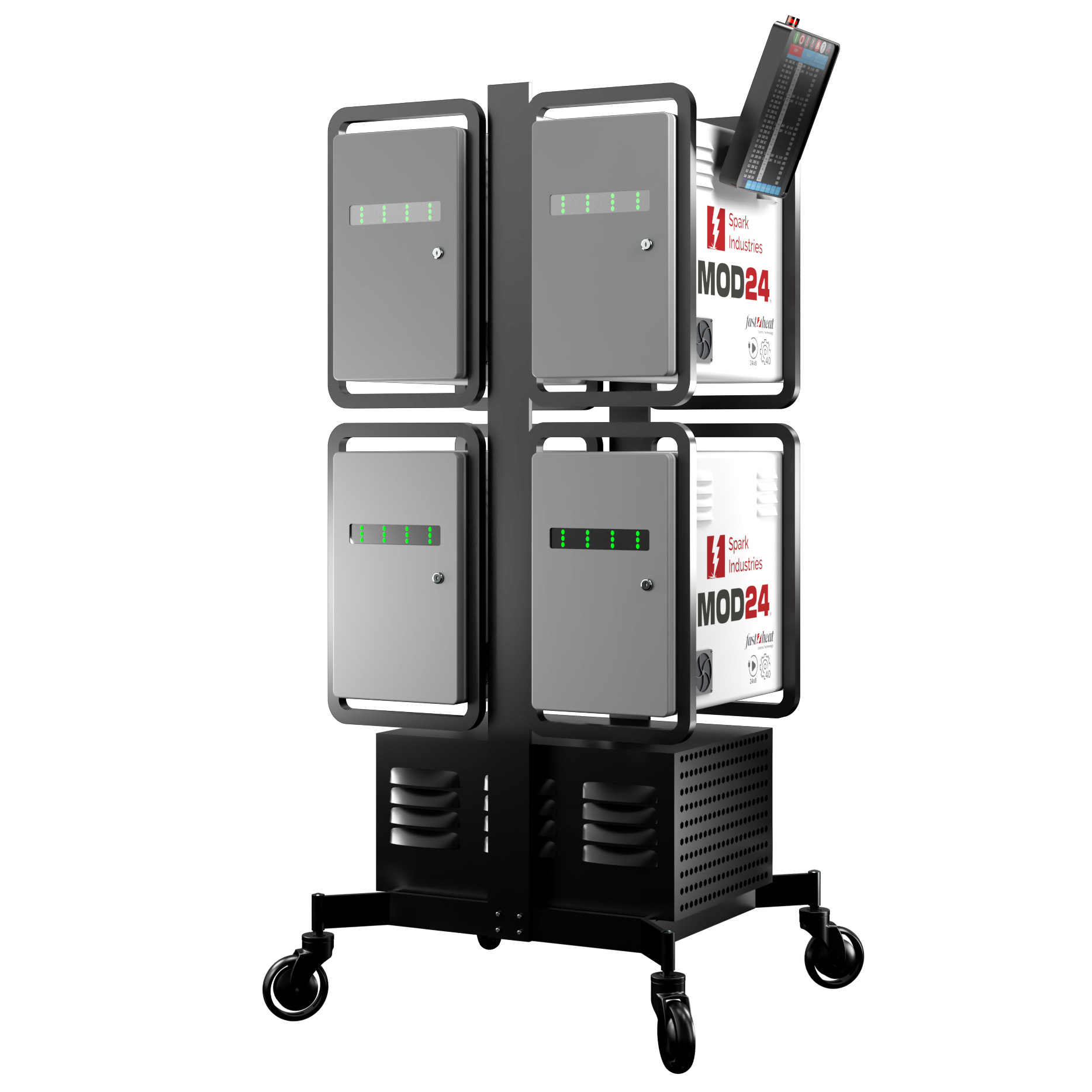
Mobile Power Rack™
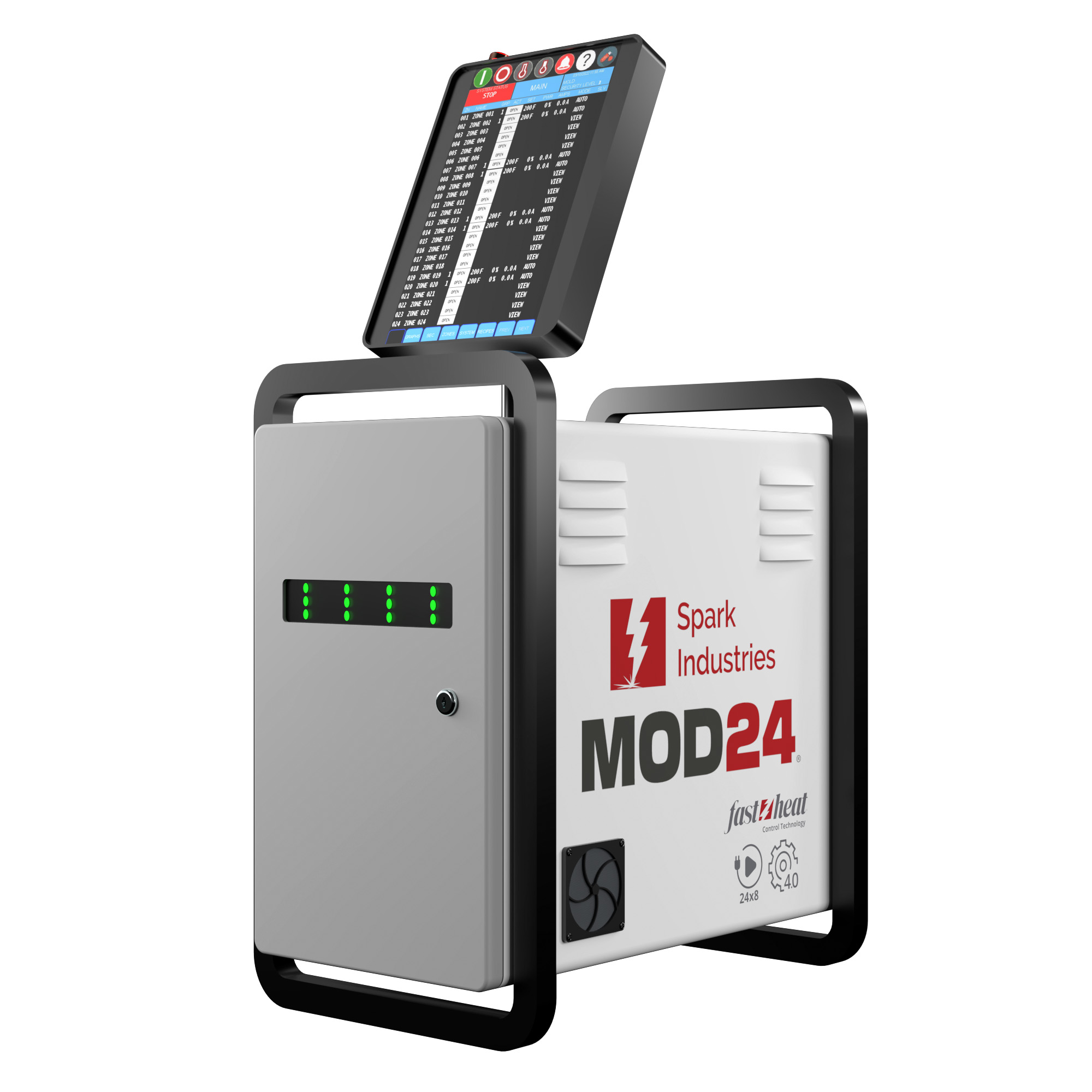
Tabletop
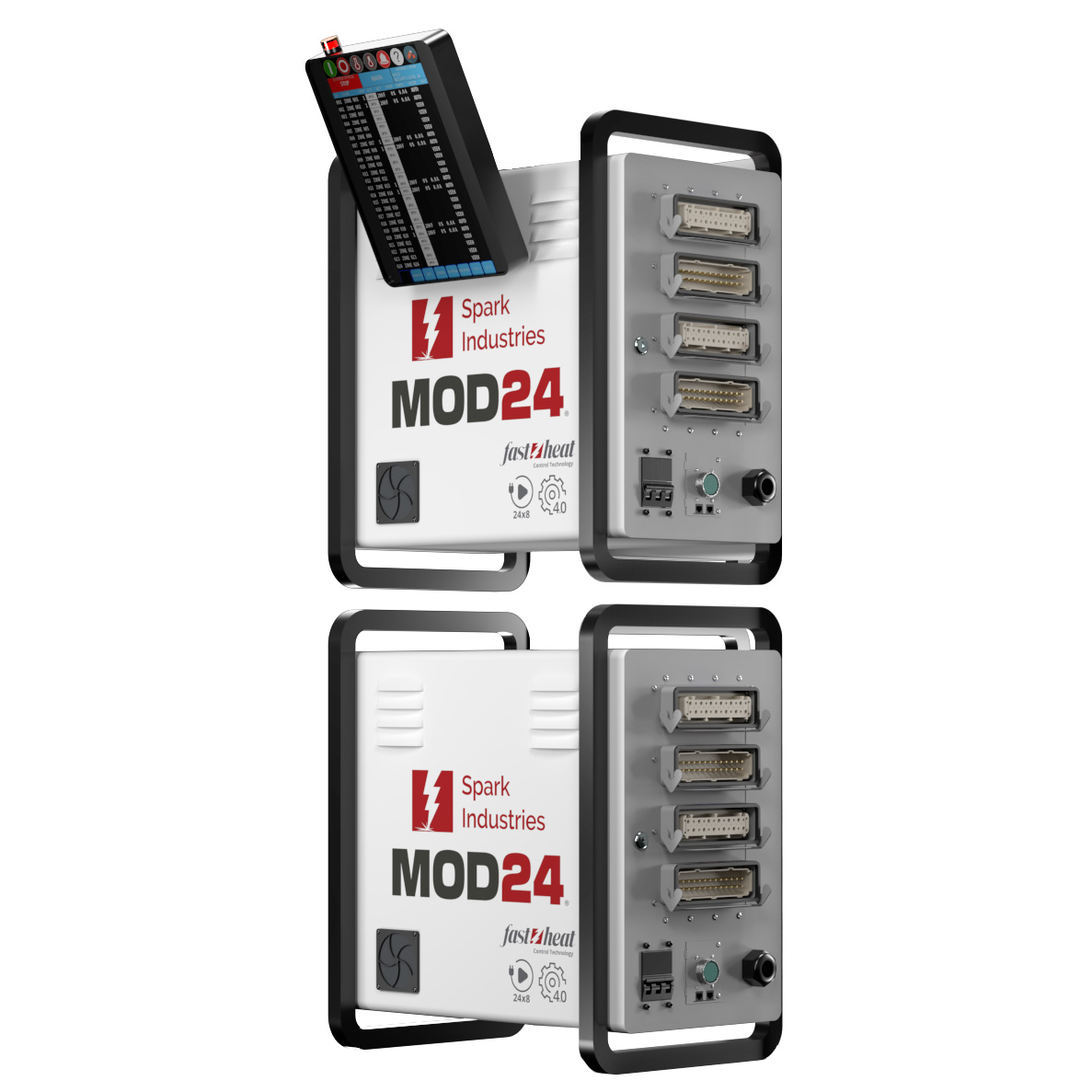
Wall or Panel Mount
The MOD24™ Hot Runner Control Story
MOD24™ is the marriage of modular, integrated, and high-cavitation hot runner controllers enhanced with modern IIoT (Industrial Internet of Things) features such as OPC-UA Euromap 82.2 data logging, remote access/control, and file transfer capabilities. It is an ideal solution for integrating with an injection molding machine and other auxiliary equipment while giving users complete modular flexibility for adding zones and mounting the controllers anywhere that is convenient.
Hot runner controllers have evolved substantially over the years. Fast Heat offered modular mainframe controllers with individual 15 or 30-amp modules for decades. These types of controllers are still commonly used today and are supplied by numerous catalog-type suppliers. They offer exceptional modularity because they are available in 1-zone, 5-zone, 9-zone, and 12-zone mainframes that can easily be combined together as needed. The downside is that each zone has its own controller. Somebody must set each control module manually and turn it on or off at the appropriate time. To save time, people often turn on all the zones simultaneously, which damages tools. These controllers call for power independent of each other, allowing peak demand to escalate. The control algorithms offer only a basic level of accuracy, which can induce too much variation in the molding process for some applications. We still supply this type of controller when requested by our affiliate, Fast Heat UK. Here are photos of this type of modular controller.
In The News:
Plastics Technology, Published 3/6/2024, Plug-and-Play Modular Hot Runner Controller
NPE2024 Show Daily – Tuesday, May 7, Page 44
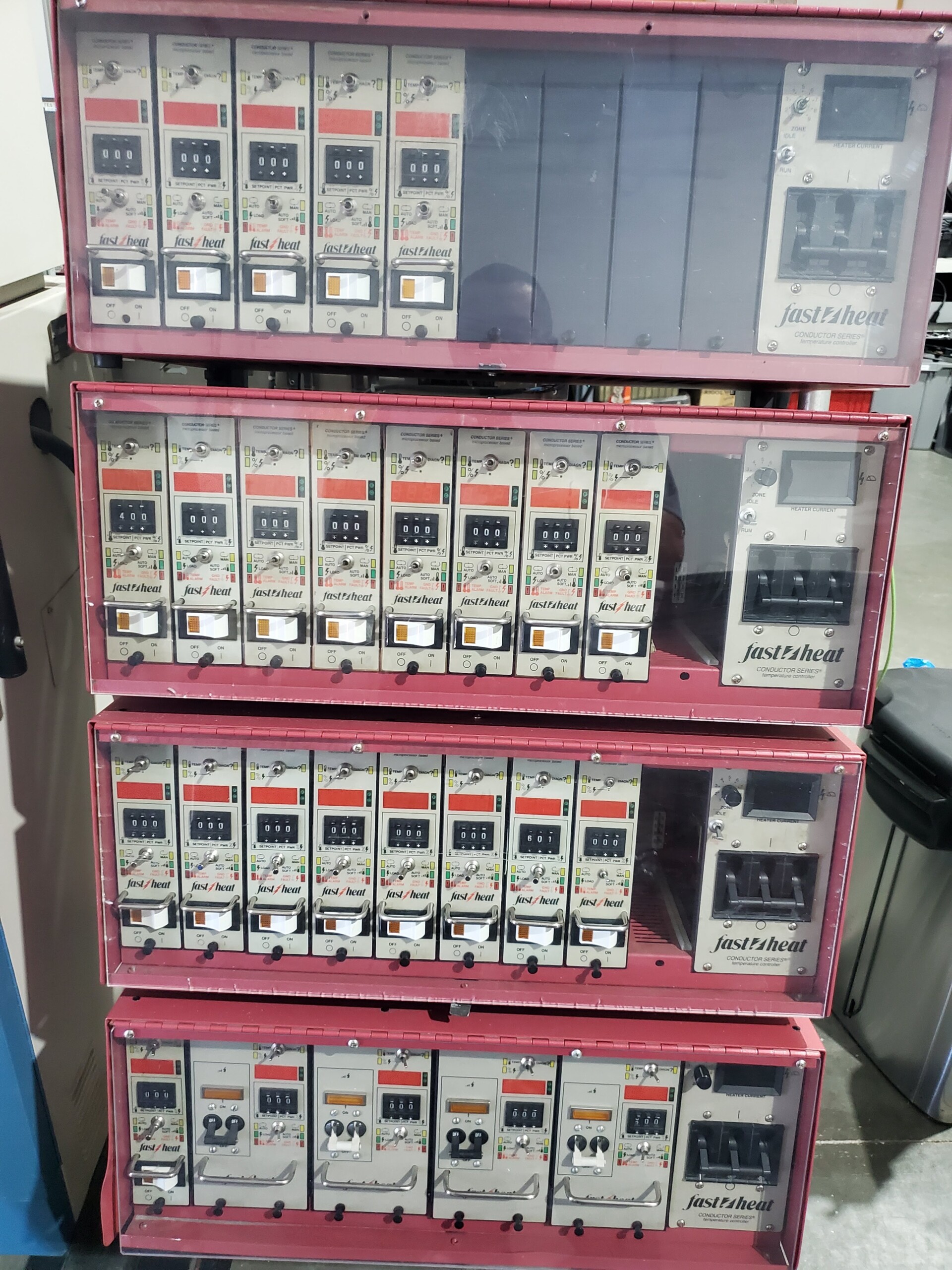
Original Conductor Series
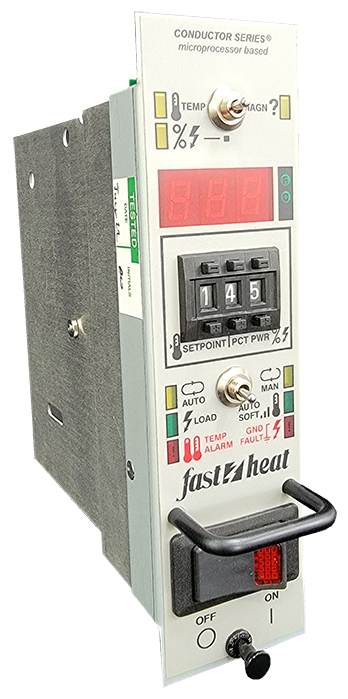
Modern day Conductor module
Integrated Hot Runner Control
Fast Heat introduced a significant innovation to the injection molding industry in 2001 called the “Pulse” hot runner controller. Much of the industry still uses this widely adopted solution for hot runner control. We inventory spare parts and provide refurbishment services as needed. The most notable advancement from modular controllers to Pulse is the single human-machine interface that displays 24 zones of set points, actual temperature, percent power, and mode. The single HMI made setting up a tool recipe easy and fast. The zones could be grouped for automatic and proper sequential start-up of manifolds first, sprue bushings or secondary masses second, and nozzles last. There was also a single-touch button for idle and boost per a saved recipe. What made the controller a success over other integrated controls was the advanced PID ideal for tight processing windows and energy management that reduced peak KW demand.
To quote one of our customers, “We need Pulse to achieve the critical gate and temperature control required to mold thin-wall parts with challenging part geometries.” – Advanced Drainage Systems, Hamilton, OH. You can read many more testimonials on our About Spark Industries page.
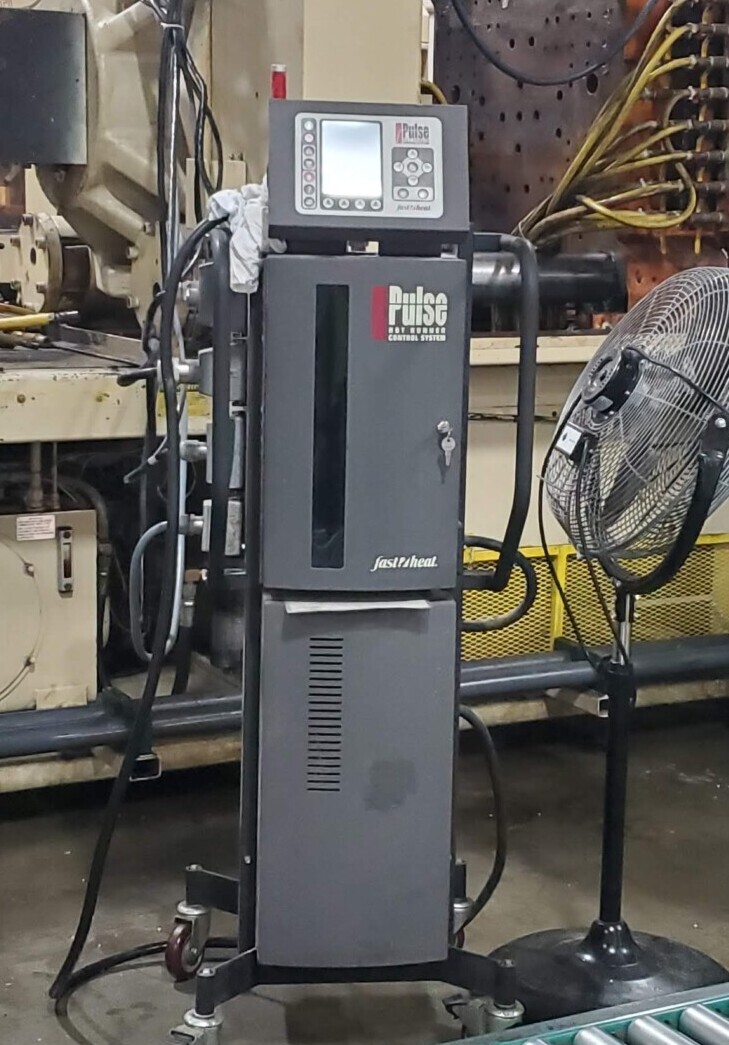
Original Pulse™ 1 still being used today
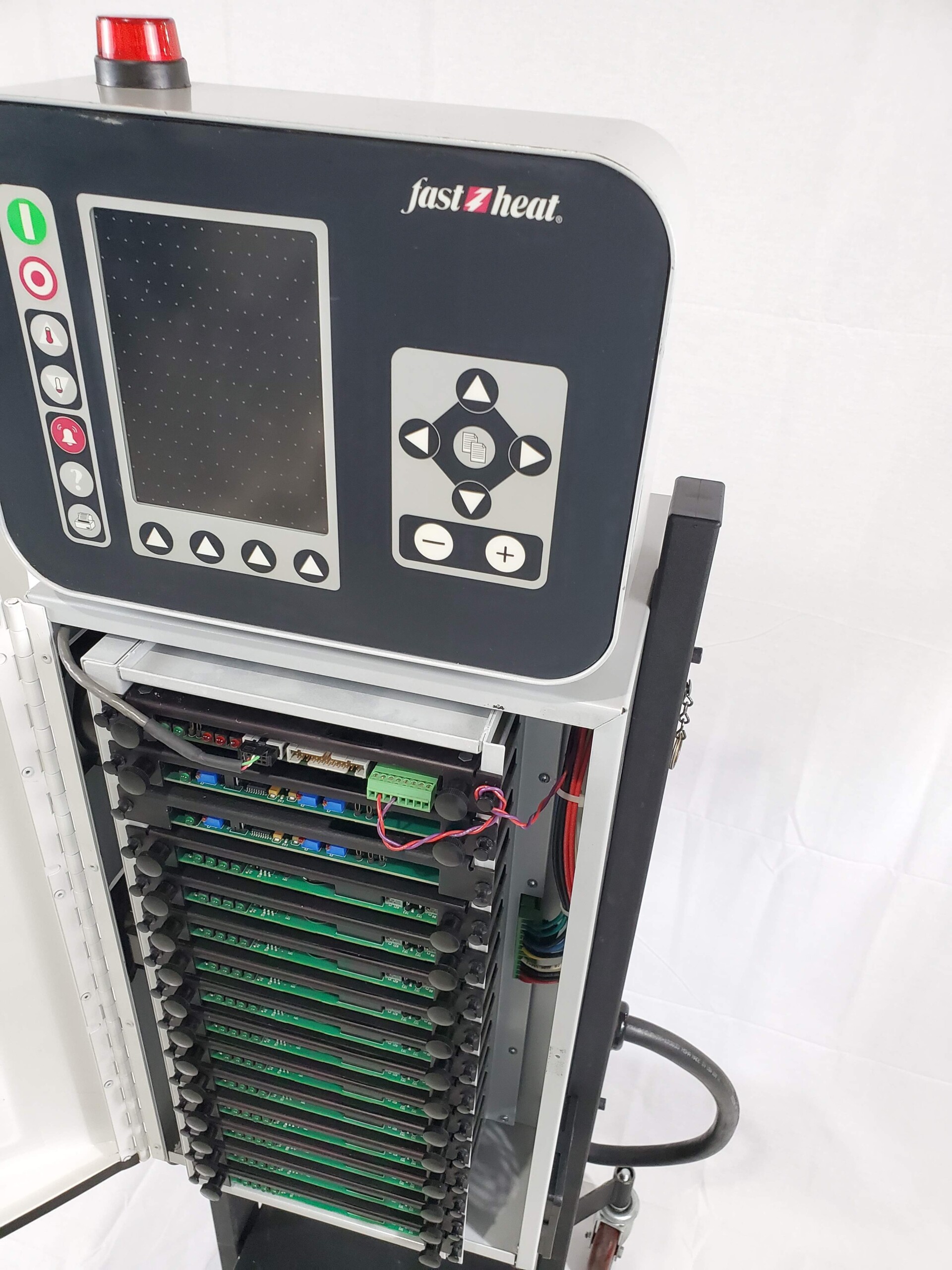
Iteration of Pulse™
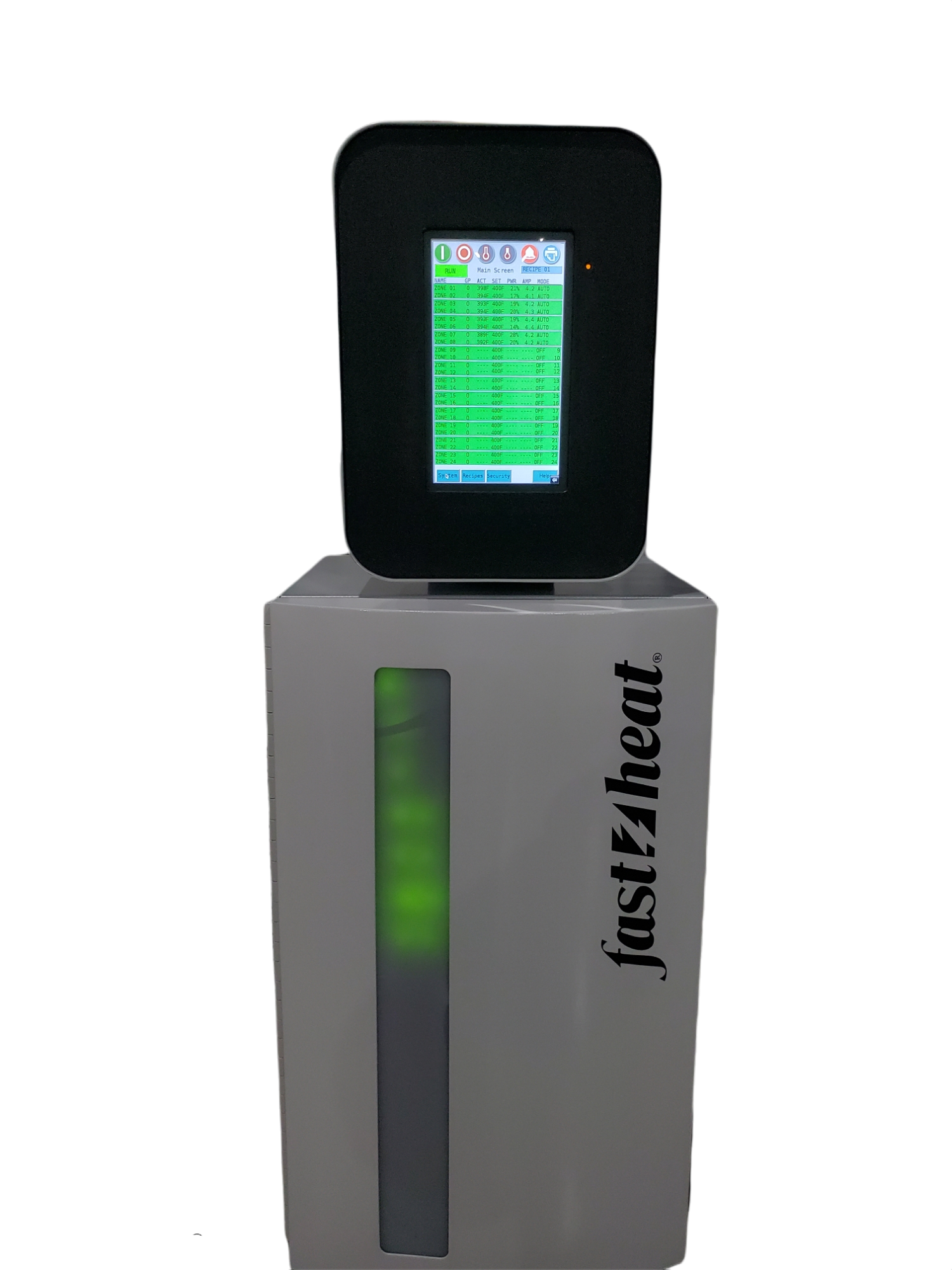
Modern day ION™
High Cavitation Hot Runner Control
In 2005, Fast Heat addressed the trend for higher cavitation hot runner systems by introducing Pulse™ II, which went up to 180 zones in combinations of 30-zone cabinets. This controller is also still used today. With more zones to manage, the HMI underwent a significant update that displayed 30 zones per page, more groups, custom naming of zones, copy/paste by line, group, or column, and some graphic displays for percent power, amperage, and temperature. We updated the display to an LCD touchscreen along the way and currently use a 10.1 high-resolution LCD touchscreen with many accolades from customers and display designers. The control algorithm and core functionality remained the same as Pulse™, an industry-leading solution. Auxiliary I/O capability and VNC Viewer have become popular features as the industry connects controllers with injection molding machines more often. We have also recently added OPC-UA for machine integration.
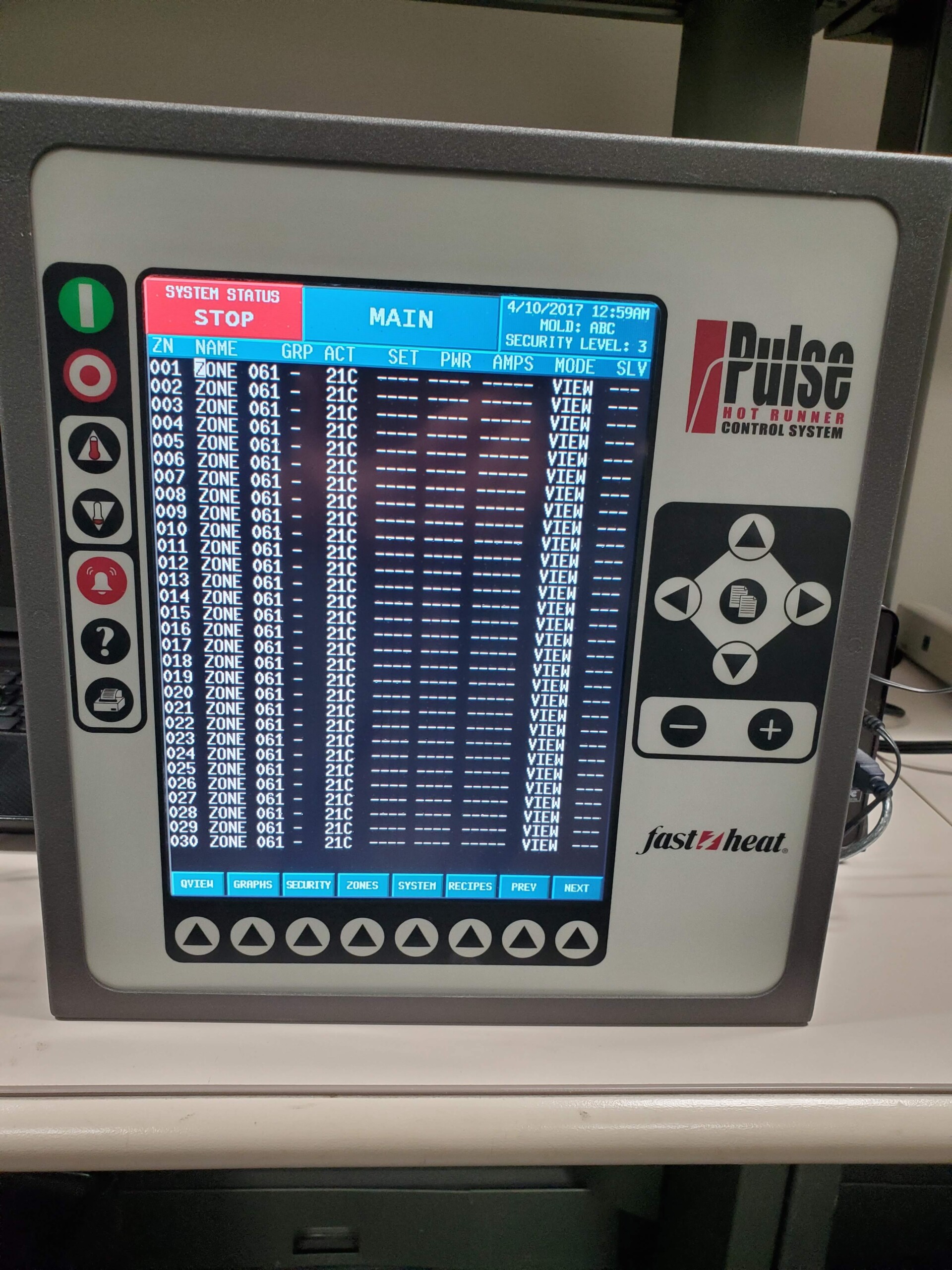
Original Pulse™ II HMI with Push Buttons
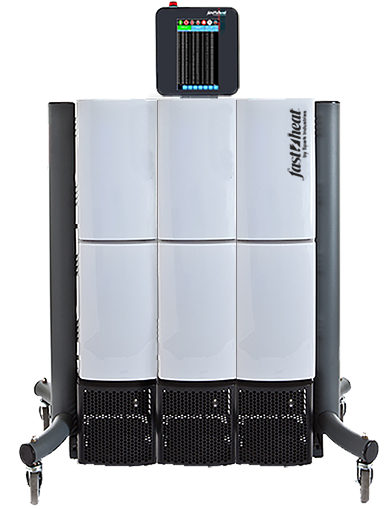
180-Zone Pulse™ II
Modern Day Pulse™, Cabinet Open