Hot runner temperature controllers are essential for optimizing injection molding processes. They provide precise control over temperatures within the hot runner system.
What Is A Hot Runner Temperature Controller?
A hot runner temperature controller is a specialized device used in injection molding systems to manage the hot runner system’s temperature accurately.
This system consists of a network of heated channels or nozzles that guide molten plastic into the mold cavity. The temperature controller’s primary role is maintaining consistent and uniform heat across these channels, ensuring the molten material’s smooth flow and even distribution.
Applications
- Electronics
- Medical
- Appliances
- Packaging
- Building
- Automotive
- Logistics
Common types of hot runner controllers available on the market include HMI-based hot runner controllers, standard plug-in hot runner controllers, and dual-zone controllers (one card controlling two zones).
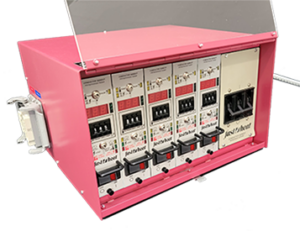
Conductor For Hot Runner System
This also includes various proprietary HMI-based hot runner controllers and more ubiquitous mainframes with single slot control cards (aka modular mainframe or “rack-style” controls).
Popular brands in the industry include Synventive, HUSKY, MASTIP, Gammaflux, EWIKON, DME, POLIMOLD, MCS, among others.
A typical hot runner controller comprises a control module, mainframe, connectors, and cables.
Types Of Hot Runner Controllers
Pulse™ Hot Runner Controller
- Configurations of 30-zone capacity cabinets up to 180-zones.
- Optional I/O for integration with the injection molding machine and other equipment
- 10.1″ LCD, 1024 x 600 resolution touchscreen HMI w/ ethernet for VNC Viewer and USB for saving screenshots
- Compact footprint
- Remote mount display option
- 240V w/ integrated transformer up to 45 KVA
MOD24™ Pulse™ Hot Runner Controller
- Modern Technology for Improved Processing, Energy Savings, and Diagnostics
- Simply Select a Recipe and Run While Protecting Your Tools
- Plug-N-Play Modules and Cabinets for Easy Expansion
- Compact and Flexible Use as Table-Top, Mobile Rack, or Wall Mount
- Best of Both Worlds – Integrates with molding machines via OPC-UA, VNC Viewer, and I/O while easily being deployed at other machines when needed.
- Industry Leading Ease-of-Maintenance and Diagnostics Along with Our MoldXChecker® and CableXChecker®
How Does A Hot Runner Temperature Controller Work?
The operation of a hot runner temperature controller focuses on precise temperature regulation and control. These controllers typically use advanced thermocouples or resistance temperature detectors (RTDs), strategically positioned within the hot runner system, to continuously monitor temperatures at key points. We’ve discussed this in detail with hot runner performance.
Using real-time temperature data collected by the sensors, the temperature controller regulates the power supplied to the heating elements in the hot runner system. By adjusting the output of these heating elements, the controller ensures that the desired temperature setpoints are maintained with exceptional precision.
Modern hot runner temperature controllers incorporate advanced algorithms and feedback systems that allow them to anticipate temperature fluctuations and proactively adjust the heating elements. This ensures stable and consistent thermal conditions throughout the injection molding process.
What Are The Biggest Advantages?
Using a hot runner temperature controller provides a wide range of benefits:
Improved Quality & Reliability: Precise temperature control within the hot runner system ensures consistent material flow and distribution, resulting in molded parts with uniform properties and accurate dimensions. This can help lower hot runner maintenance.
Higher Flexibility: The ability to precisely control the temperature of individual hot runner nozzles provides greater flexibility for molding complex parts with varying geometries and material requirements.
Lower Cycle Times & Added Efficiency: Efficient temperature regulation allows for faster cooling of molded parts, reducing cycle times and boosting overall production efficiency.
Reduced Material Waste: By maintaining uniform heating and distribution, hot runner temperature controllers minimize material waste by reducing defects such as sink marks, warpages, and short shots.
Cost Savings: Improved efficiency, shorter cycle times, and reduced material waste collectively lead to significant long-term cost savings in injection molding operations.
Easier To Start: Without runners to remove, the auto cycle occurs faster and more frequently, resulting in an easier start.
Hot runner systems deliver exceptional injection molding results, with temperature controllers as the core of their operation. These controllers enable the system to perform efficiently, minimizing waste and enhancing product quality.
Fast Heat By Spark Industries is your trusted source for hot runner controllers, cables, sprue bushings, mold boxes, and more. Be sure to visit our online shop. Need a custom quote? Click here.