Hot runner cable connectors come in a wide range of specifications with some being much better than others. Our recent article in MoldMaking Technology magazine calls attention to the top 5 problems we typically see in the field. These include:
- Pushed-Back or Bent Pins
- Pushed-Back Inserts
- High Amp Deterioration
- Loose or Broken Latches
- Missing or Loose Ground Wire Connections
The anatomy of connectors is shown in the featured image. Hoods come in low and high profiles with top or side cable entry and one or two locking levers. Male contacts should be machined but the smaller 25-pin variety can be found in a rolled and crimped design, which is not recommended. Male pins (contacts) and female inserts are press-fit into their related insert bases. Housings are specified to match the mating housing with either one or two locking levers.
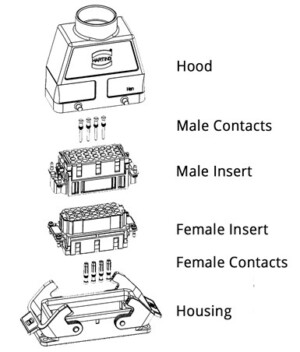
hot runner cable connector anatomy
To summarize the article, we strongly encourage molders to use the 24-pin, machined and molded male and female connectors shown here.
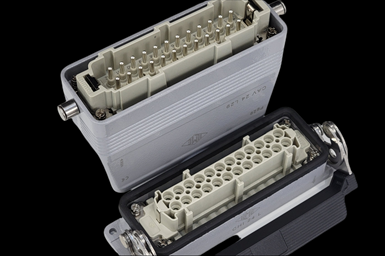
24-pin hot runner connectors
Unfortunately, a lot of molders are stuck with old industry standards that utilize 25-pin connectors. The pins are very delicate (1/16-inch diameter exposed) and can easily be bent or pushed back when being mated to a female connector on a mold box, cable or hot runner controller. The same thing can happen with the female inserts because the metal inserts are only press fit into the connector. These 25-pin connectors are also only rated for 10 amps, yet many shops use them for manifold circuits that can easily exceed 15 amps.
Routinely maintaining loose or broken latches would seem to be a simple thing. However, it’s very common to see connection issues as a result of poor maintenance.
Lastly, it is very important to make sure the ground wire is connected on both ends of a hot runner cable.
See more about hot runner cables.
Learn about cable diagnostics.
Common Hot Runner Cable Connection Problems
Related – The Ins and Outs of Hot Runner Temperature Control