Hot Runner Productivity Series
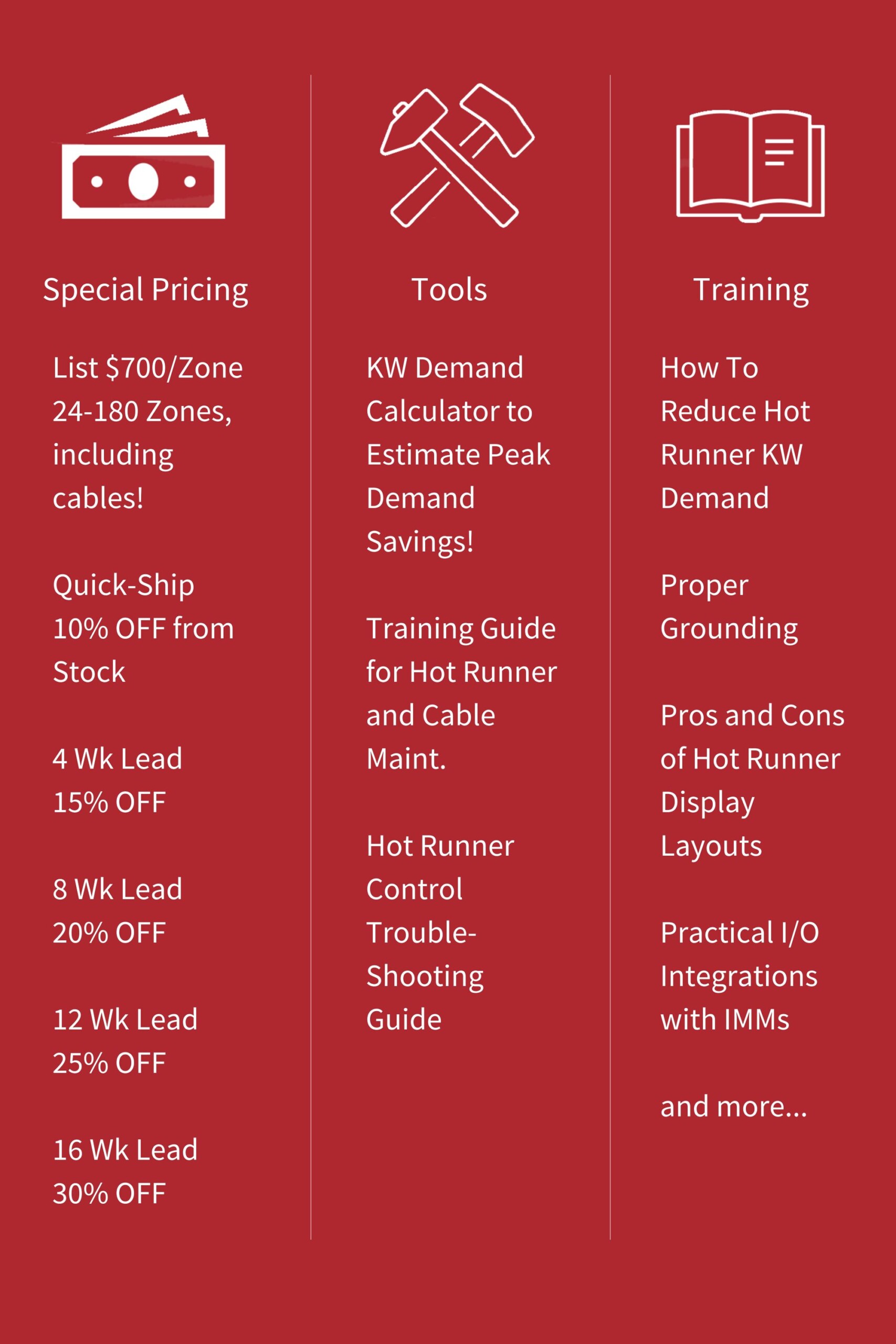
Register for special pricing, tools, and training to help with hot runner processing, energy savings, and maintenance.
High-Cavity Hot Runner Productivity Series Highlights
This 5-post series follows a normal order of events on the molding floor from before you start molding to more advanced molding cell automation.
- kW Demand – We’ll show you how and why you should reduce kW demand.
- Maintenance – This covers preventative maintenance of hot runner systems, cables, and controllers.
- Troubleshooting – How should you react when alarms or other things go out of normal range?
- Processing – What’s happening behind the scenes in your hot runner system, and why does it matter for processing (better cavity-to-cavity balance, lower operating temperatures)?
- Molding Cell Integration – How could communications between your hot runner controller, the injection molding machine, or other auxiliaries optimize your molding cell?
kW Demand
High-cavity hot runner systems can consume a lot of electricity. When you register for this productivity series, we’ll send you an Excel spreadsheet to calculate the total system amps for your tools. For example, a recent customer figured that the total system amps for their 72-zone hot runner system is 359.7 amps! We’ll show you how our Pulse hot runner controllers enable you to minimize start-up kW demand and automatically limit peak amp draw by up to 67% while maintaining precise temperature control during set-point operation.
Maintenance Training
Maintaining hot runner systems and cables can be a tedious job. We’ll send you a training guide to show you how to use our MoldXChecker™ and CableXChecker™ to save you time and ensure 100% accurate system and cable testing results. And, whether or not you use our tools, this guide will help show you how important it is to check for opens, miswires, and dangerous shorts.
Hot Runner Control Troubleshooting
Preparation precedes success! We created a production-ready checklist to help you and your team hit the ground running. Proper grounding is the common denominator at each connection point throughout the electrical supply. Both veterans and new professionals will want to take note. Our checklist is a proactive method that we shared in a Plastics Technology Webinar in 2022. It’s a big help to have a troubleshooting guide handy when you’re in production, and something goes wrong. We’ll include this in the email series as well.
And more, including Hot Runner Control Display Layouts and Practical I/O integrations with IMMs.
Please use the form above to register for these great resources and take advantage of some great pricing opportunities.
Related links: